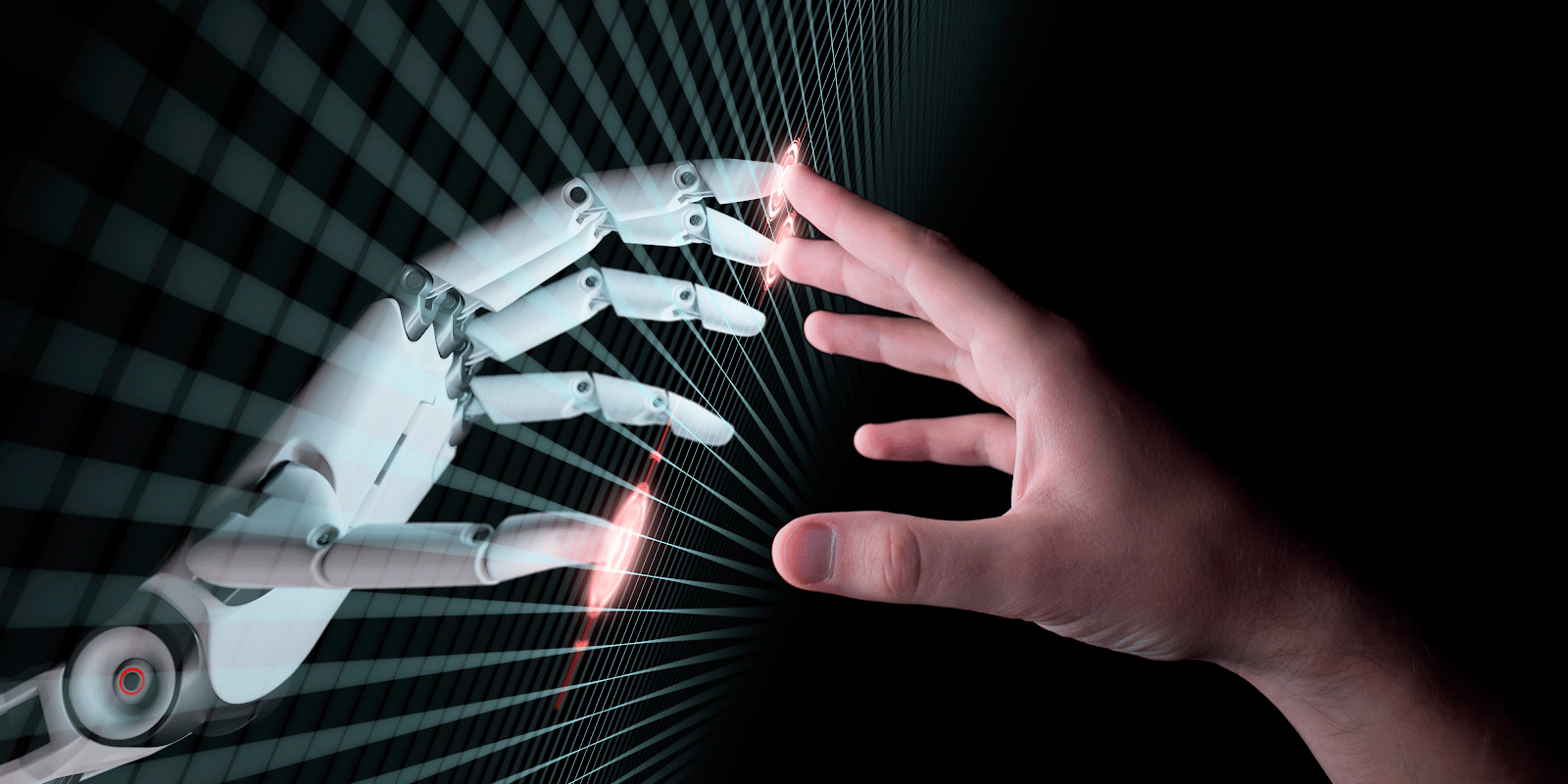
A Cidade do Cabo é às vezes chamada de “Vale do Silício da África do Sul”. No entanto, foi uma surpresa agradável saber que a Atlantis Foundries tornou-se uma líder da indústria de fundição não apenas na África, mas no mundo todo, usando inteligência artificial (IA) e aprendizado de máquina para obter zero defeitos nas peças que entregavam a seus clientes na Europa e nos Estados Unidos.
Nesta entrevista, Pieter du Plessis, o CEO da Atlantis Foundries na época dessa iniciativa, conta a história (que você pode ler ou assistir abaixo) de como eles usaram a IA para resolver um problema estratégico do negócio. Considerando toda a hype que a Indústria 4.0 tem recebido, existem algumas lições valiosas aqui de alguém que realmente fez a IA funcionar no mundo real.
Há muito a aprender com o que Pieter compartilha conosco, mas gostaria de destacar um aspecto em particular. Tornou-se moda usar o termo "ir além do lean” na pressa de comercializar as tecnologias da Indústria 4.0. Com certeza, essas novas tecnologias estão mudando o jogo e não podem ser ignoradas, mas acho que referir-se a elas como "indo além do lean” é o resultado de um mal-entendido fundamental sobre o que é o pensamento lean.
Antes de introduzir a IA, a Atlantis Foundries investiu em melhoria contínua por muitos anos para melhorar sua taxa de defeitos e alcançar o padrão da indústria. Isso significa que, no momento em que começaram a experimentar com a IA, já havia uma cultura de solução de problemas na organização sobre a qual eles poderiam construir. Você ouvirá Pieter referir-se à IA como outra “ferramenta” na jornada de melhoria. Em outras palavras, assim como usamos os cinco porquês como uma ferramenta para encontrar as causas raízes, agora existe essa ferramenta muito poderosa chamada IA que pode ser usada em situações em que humanos não conseguem lidar com a quantidade de informação que precisa ser processada.
Como qualquer outra ferramenta de solução de problemas, a IA pode ser usada de forma incorreta ou inadequada se você não aplicar o lean ao problema em questão. Perguntar qual problema precisamos resolver tem que ser o primeiro passo, o que informará nossa solução de problemas e a tornará efetiva. A Atlantis Foundries pensou muito cuidadosamente sobre essa questão, e isso a guiou quando ela descobriu como explorar a IA.
Essa história nos mostra como o pensamento lean é importante para o sucesso de novas tecnologias, como aprendizado de máquina e IA.
Anton Grütter: Pieter, você pode nos apresentar a Atlantis Foundries?
Pieter du Plessis: A Atlantis Foundries é um subproduto da Atlantis Diesel Engines, uma fábrica de motores comprada no final dos anos 70. A Atlanta Diesel Engines faliu, mas a Atlanta Foundries foi comprada pela Daimler/Mercedes Benz para continuar fundindo blocos de cilindros para caminhões. A Daimler já tinha uma fundição em Mannheim, na Alemanha, mas com as severas leis ambientais no país, ela não conseguia expandir sua capacidade. Por isso, ela comprou a Atlantis Foundries em 1999 para fundir essas peças. A Atlantis Foundries passou a exportar todos os seus motores para clientes no Reino Unido, EUA, Coréia do Sul e Alemanha.
AG: Você pode nos explicar por que a qualidade era tão importante para a Atlantis Foundries?
PDP: Estar tão longe dos clientes que servimos significa que, se você tiver algum problema de qualidade detectado nas operações de usinagem na fábrica do cliente, todo o oleoduto poderia estar contaminado. O custo de procurar defeitos de qualidade no oleoduto – o que pode levar de seis a oito semanas – é enorme. É por isso que entregar a qualidade certa na primeira vez é tão importante para nós. Nossos custos de qualidade são significativos.
AG: Como você tentou resolver esse problema de qualidade inicialmente?
PDP: Com as ferramentas clássicas de qualidade, como controle estatístico de processo, planos de controle, folhas de processo e assim por diante. Qualquer coisa que as empresas tradicionais fariam para melhorar a qualidade. No entanto, chegamos a um ponto em que não conseguimos mais avançar, porque o ciclo de feedback era muito longo, e o processo era muito complicado e cheio de variáveis. Encontrar um padrão nessas variáveis era difícil. Uma fundição de referência que fabricava as mesmas peças que nós normalmente tinha entre 4 e 8% de sucata, e estávamos em torno de 6% – com um acréscimo de 1,5% no site do cliente. Nós estávamos no meio do caminho.
AG: O que fez vocês decidirem experimentar com aprendizado de máquina?
PDP: Queríamos prever qual peça seria defeituosa lá no cliente, nos EUA ou na Alemanha, para nem enviá-la. Como o defeito é uma função do processo, deve haver um padrão no processo que possa ser reconhecido. Dessa forma, você sabe que se o processo for de certo modo, produzirá uma peça defeituosa. Estamos falando de defeitos que estão escondidos e não podem ser vistos fisicamente, nem encontrados com métodos ultrassônicos, devido a seu tamanho e volume. Queríamos prever, com base em qual era o processo naquele momento, se uma peça seria sucata ou não. No final, tivemos uma taxa de sucesso de 70%. Diríamos “jogue essas 10 peças fora” e sabíamos que sete delas teriam se tornado sucata. Sabíamos que jogaríamos três peças boas fora, mas o custo associado era insignificante em comparação com o que se usava nos EUA.
AG: Quando você tomou essa decisão?
PDP: Começamos com o aprendizado de máquina em março de 2017, dando ao “Data Prophet” [especialistas em aprendizado de máquina na Cidade do Cabo] 18 meses de dados de processo e de resultados de qualidade (internos e externos) que tínhamos acumulado.
Não precisamos gerar novos dados. Apenas pegamos os dados que tínhamos diariamente, mas que nunca usamos. A tarefa mais difícil é combinar os dados com a peça que você faz: normalmente usávamos séries temporais – verificando o processo a cada meia hora, a cada 40 minutos ou uma vez por dia –, mas nossa taxa de produção era de uma peça a cada minuto. Costumávamos fazer 700 peças por dia, um número enorme, se você pensar bem. Dos 180.000 motores de caminhão que já havíamos construído, no início só tínhamos dados perfeitamente compatíveis para 7.000. Então, usamos esses dados para construir o primeiro modelo. À medida que você alimenta mais dados toda semana, o algoritmo aprende mais. Você também pode começar a fazer seus testes para corresponder às peças exatas, o que é bastante crítico para o processo: quando fazemos a peça número 1 ou número 20, sabemos quais parâmetros devemos verificar, em vez de checar aleatoriamente em intervalos regulares. Essencialmente, nossos métodos de teste mudaram.
AG: Como isso funciona na prática?
PDP: Existem vários tipos de inteligência artificial e aprendizado de máquina. Há aprendizado supervisionado e não supervisionado. Com o aprendizado não supervisionado, a resposta não é conhecida; você dá à máquina os dados brutos e encontra os padrões lá. Com o aprendizado supervisionado, informamos à máquina se o resultado foi uma peça boa ou ruim e fornecemos os parâmetros do processo para cada um; o algoritmo usa força bruta calculando todas as iterações até chegar a uma resposta (no entanto, tínhamos 185 variáveis no processo, então você pode imaginar a complexidade).
AG: Houve problemas com as pessoas? Eles aceitaram isso?
PDP: Nós tivemos problemas. Havia muitos que não acreditavam, inclusive eu. Eu era muito cético no começo, porque não entendia como os especialistas podiam apenas solicitar dados sem entender nosso processo. Alguns dos engenheiros temiam pelo seu trabalho e achavam que a IA iria substituí-los. Eu subestimei o fato de que, segundo o que eu achava, pessoas inteligentes e bem-educadas não teriam medo da IA. Demorou um pouco para as pessoas a entenderem e usarem, mas os resultados foram espetaculares.
Usando o modelo, queríamos prever qual peça viraria sucata nos EUA e, na segunda fase, aprender o que tínhamos que fazer para não fabricar peças que virariam sucata. O modelo que previa sucata passou a prescrever o processo. Ele pegou parâmetros do processo e calculou a região para todos eles (min 11), o que significava que os limites do nosso processo foram espremidos significativamente, e alguns deles foram ajustados. A combinação dessas duas coisas nos permitiu, no segundo semestre de 2017, obter zero defeitos em três plantas por três meses seguidos. Isso foi inédito.
Conversei com algumas pessoas recentemente, e essa tendência continua – mesmo que zero defeitos não seja atingível o tempo todo, porque os parâmetros do processo ficam muito apertados ao longo do tempo. E é por isso que as pessoas sempre serão importantes nessa coisa de IA: elas terão que analisar esse relatório e decidir o que precisam fazer na máquina para que ela alcance o resultado desejado. Você não pode dizer a uma máquina: “Você não pode fazer isso”. As máquinas não são tão inteligentes. A noção de que a IA irá substituir todos os seres humanos é uma falácia. Talvez daqui dois séculos. Certamente muito mais tarde do que muitas pessoas pensam.
AG: Que conselho você tem para pessoas interessadas na Indústria 4.0?
PDP: Acho que muitas pessoas estão tendo dificuldade para entender o que a Indústria 4.0 realmente significa. Eles dizem: “Temos dados, vamos fazer algo com eles”. Para mim, essa abordagem está errada. Eles devem se perguntar qual é o maior problema em seu negócio e como essa ferramenta adicional pode ajudá-los a atingir sua meta. Na Atlantis Foundries, por exemplo, queríamos evitar sucata nos EUA e na Alemanha. Uma vez que conseguimos prever qual peça seria defeituosa, queríamos descobrir o que tínhamos que fazer para evitar que elas fossem fabricadas. Você precisa de um objetivo claro. Apenas fazer a Indústria 4.0 por fazer é uma perda de tempo.
AG: Cada vez mais se fala sobre ir “além do lean” nos dias de hoje quando se discute tecnologias como a inteligência artificial. O que você acha disso?
PDP: Na minha opinião, o lean busca simplificar processos, reduzir desperdícios e tornar o trabalho repetível e eficiente. Para mim, a IA é outra ferramenta que permite que você faça isso. Não é uma bala de prata; é apenas outra ferramenta. À medida que me envolvi mais com isso, percebi rapidamente o quão longe estamos de máquinas fazendo tudo sozinhas sem a necessidade de envolver pessoas. Estamos incrivelmente longe disso. O aspecto humano é importante, porque parte do processo são as influências humanas. Se um operador não seguir as regras, você poderá ter toda a inteligência artificial do mundo, mas ainda assim terá um problema. Então, para mim, a IA não está além do lean (em inglês)... ela é outra ferramenta para o lean.