No verão de 2018, Sølve Kiviranta estava sentindo a tensão do combate periódico a
incêndios que ele enfrentou desde que assumiu o cargo de gerente de fábrica da Mowi, em
Eggesbønes. Ele não era o único.
Sølve passou o verão enfrentando uma série de desafios que surgiam na fábrica de peixes,
juntamente com sua equipe de gestão. Eles estavam exaustos. Algo precisava mudar.
A fábrica, uma das maiores do mundo do setor, está localizada em Eggesbønes, Fosnavåg, a
cerca de uma hora de carro de Ålesund, na costa oeste da Noruega. A fábrica havia experimentado um
começo falso com o lean depois que uma tentativa liderada por uma consultoria em 2012 foi rapidamente
interrompida. As ferramentas foram implementadas, mas sem o espírito kaizen, pouco aconteceu.
Apesar disso, Sølve sabia que o lean poderia ser o remédio certo, desde que fosse administrado
corretamente. Sua experiência em empregos anteriores e a teoria que ele aprendeu em livros e treinamento de
liderança lean moldaram sua crença de que o lean tem tudo a ver com as pessoas e que a
transformação tinha que começar com ele mesmo.
Juntamente com sua equipe de gestão e em estreita colaboração com o veterano gerente de
produção Hans-Jakob, Sølve começou a tomar algumas decisões difíceis. Uma
delas foi trazer Marcin, que tinha experiência em transformações lean anteriores, mas estava
ficando cada vez mais frustrado com o impasse que estava enfrentando na empresa em que trabalhava na época.
Outro ponto de virada foi a percepção de que se a Mowi Eggesbønes quisesse ter sucesso com os
projetos de automação e digitalização que estavam por vir, as habilidades de solução
de problemas teriam que ser desenvolvidas.
A Sølve precisava construir capacidades de pensamento lean na organização rapidamente para
visualizar e reduzir o desperdício. Não fazia sentido automatizar e digitalizar processos
desnecessários que não funcionavam. Uma transformação lean é, antes de tudo, uma
transformação cognitiva: aceitar, como líderes e operadores, que não sabemos o que
não sabemos e que para mudar os outros, primeiro precisamos mudar a nós mesmos.
Seja a mudança que você quer ver
Mindaugas, Inger e os demais gerentes intermediários da fábrica viram desde cedo que essa
mudança seria diferente. Não haveria oportunidade de se esconder, e eles precisavam estar à
altura da ocasião.
Para Inger, essa foi uma mudança bem-vinda. Tendo começado na fábrica em 2004, ela viu
vários programas de mudança começarem e pararem. Mas ela também enxergava a necessidade
de melhorias, tendo se cansado do constante combate a incêndios e de vir trabalhar sem saber o que esperar.
Sølve e Hans-Jakob sabiam que precisavam envolver e desenvolver seus gerentes intermediários para ter
sucesso, e Inger estava pronto para aceitar o desafio.
Com mais responsabilidade, mas também mais liberdade, ela trabalhou com Marcin para treinar a si mesma e seu
departamento na solução de problemas. Em vez de começar com as ferramentas, entretanto, Marcin
e Inger foram à procura de problemas. Começando com aqueles que simplesmente não pareciam ir
embora – o tipo de problemas “nós temos isso há 5 anos”. Cada problema apresentava
uma oportunidade de aprender diferentes ferramentas lean como contramedidas e aprendizagem.
Após um período de problemas de qualidade, Marcin e Inger decidiram ir ver (genchi genbutsu)
para entender melhor por que isso estava ocorrendo. Ao observar os colaboradores no departamento de filés e
estudar seu trabalho, eles perceberam que os padrões não eram fáceis de entender, o que
significava que treinar os operadores no trabalho de agregação de valor não era fácil.
Inger percebeu que precisava treinar mais do que simplesmente as mãos dos membros de sua equipe; ela precisava
mudar sua abordagem de gestão para liberar a criatividade dos operadores e líderes de equipe. Marcin
sugeriu que eles fizessem um curso de Instrução de Trabalho para aprender a criar bons padrões
e desenvolver a conscientização no departamento sobre a necessidade de padrões e treinamento.
Apesar do calendário de treinos ter sido ligeiramente prejudicado devido à pandemia da Covid-19, eles
conseguiram realizar um piloto com grande sucesso. Os participantes, tanto operadores experientes quanto
líderes de equipe e gerentes de departamento, entenderam imediatamente que desenvolver e treinar operadores
de acordo com os padrões seria benéfico para todos. Já na primeira sessão,
experimentaram uma dinâmica diferente na equipe, talvez percebendo que o processo em que trabalham exige
excelentes competências e atenção aos detalhes. De repente, todos os tipos de dicas e truques
vieram à tona. De fato, o treinamento de Instrução de Trabalho foi fundamental para
alcançar a estabilidade do processo.
Com o tempo, uma cultura kaizen foi se desenvolvendo na Mowi Eggesbønes. Sølve estava criando
um senso de urgência e uma necessidade de melhoria, elevando o nível da organização ao
desafiar os gerentes a olhar além dos padrões e estruturas estabelecidos. O mantra era: “Alvo,
Desafio, Problema, Kaizen”. Foi criada uma obeya de gerenciamento
diário numa das principais áreas da fábrica. Lá, cada colaborador podia enxergar
como o trabalho de solução de problemas e melhoria estava contribuindo diretamente para a
estratégia abrangente do negócio. Sem o conhecimento e a experiência dos operadores, não
havia chance de os gerentes transformarem seus departamentos.
Limpeza, limpeza, limpeza
Após uma discussão com Sølve, Mindaugas se desafiou a se tornar um líder melhor. Ele
olhou para si mesmo e viu um líder que estava controlando e comandando. Este não é quem ele
queria ser. Para ter sucesso em transformar seu departamento no melhor departamento de limpeza da Mowi, ele primeiro
precisava se transformar. Seu novo mantra passou a ser: “Se eu cuido das pessoas, as pessoas vão cuidar
da fábrica”.
Passou a ouvir, discutir e refletir mais com os colaboradores de sua área, envolvendo a equipe no
planejamento, na conversa sobre qualidade e na discussão do que é um bom trabalho. À medida que
esse processo continuava, Mindaugas e sua equipe perceberam que para ser o melhor departamento de limpeza, eles
teriam que abraçar o conceito de que o diabo está nos detalhes. Eles começaram a padronizar e
resolver problemas, ao mesmo tempo em que constantemente elevavam a barra um pouco mais. Diante das
condições difíceis, principalmente nos turnos da noite, as ferramentas lean ajudaram a acelerar
esse departamento ambicioso.
Durante um período de três anos, a equipe passou da limpeza reativa para a limpeza preventiva
sistemática. Durante esse período, o absenteísmo caiu de 20% para 2% e agora eles estão
superando em 10 vezes o KPI de “melhores práticas” da indústria para limpeza, cobrindo
quatro vezes mais metros quadrados em comparação com outros departamentos de limpeza e ultrapassando
os limites do que é considerado classe mundial na indústria. Ao se transformar, Mindaugas transformou
uma equipe de 24 pessoas.
Subindo a curva de aprendizagem, um problema de cada vez
Quando o gerente de qualidade saiu da empresa, o restante da equipe do departamento de qualidade ficou com a
difícil tarefa de cuidar da garantia da qualidade e dos relatórios. Assim como seus colegas de
produção, eles foram solicitados a estabelecer um plano anual de atividades relacionadas à
qualidade. Apoiados por Marcin, eles conseguiram sair da zona de conforto e entrar na zona de aprendizagem, lidando
com revisões internas e externas e, ao mesmo tempo, apoiando a organização na garantia e no
controle da qualidade.
Ao mesmo tempo, Marcin estava auxiliando os líderes de departamentos na formação de
círculos de qualidade, formando equipes e incentivando a participação voluntária. Muitos
aderiram, mas novamente a Covid desacelerou a iniciativa. Mesmo assim, isso permitiu que mais e mais pessoas
desenvolvessem seus conhecimentos e competências por meio da solução de problemas, e a
fábrica de Eggesbønes gradualmente começou a passar de uma organização de combate
a incêndios para uma organização que olha para o futuro. Como disse um dos gestores durante
nossa visita, “não me estresso vindo trabalhar, porque sei que estamos lidando com os problemas mais
cedo. Estamos trabalhando de forma muito mais estruturada com a solução de
problemas”.
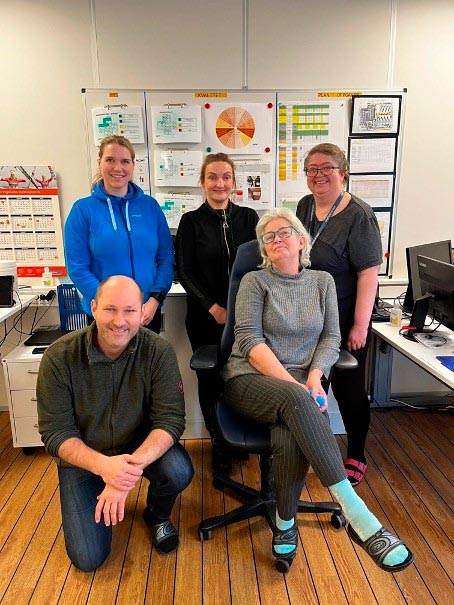
O poder das pessoas na automação
Paralelamente à transformação das pessoas, a fábrica de Eggesbønes também
foi um campo de testes para novas tecnologias na Mowi. Um exemplo disso foi a integração de um sistema
AGV no departamento de distribuição. No início, as pessoas estavam céticas e preocupadas
com seus empregos e tinham preocupações legítimas sobre a adequação de um sistema
automatizado mais rígido. Entretanto, com uma política de portas abertas no compartilhamento de
informações e esforços para engajar as pessoas, as operadoras passaram a contribuir com a
implantação do sistema AGV – novamente, trazendo valioso conhecimento tácito e
também registrando sistematicamente problemas com o sistema.
Ao mesmo tempo, muito tempo e esforço foram dedicados ao treinamento e desenvolvimento dos colaboradores,
dando-lhes competência e confiança para operar o novo sistema. Ao usar ativamente as ferramentas lean,
como 5S, padronização e solução de problemas, o departamento estava mesclando
automação com desenvolvimento de pessoas.
Junto com a implantação do sistema AGV, surgiu uma cultura de solução de problemas. Agora
eles estão usando padrões para integrar novos operadores na equipe de filé de maneira
semelhante, enquanto todos estão contribuindo voluntariamente com ideias de melhorias e
correções.
Desenvolvimento da cadeia de formadores
Reunindo-se em cadência regular, o pessoal de Eggesbønes pode agora discutir os números
diários de produção e os problemas no gerenciamento diário, enquanto a equipe de
liderança pode se concentrar em melhorias estratégicas, que são acompanhadas na
reunião
semanal de gestão, e no acompanhamento de suas principais atividades, com os planos anuais, uma vez
por
mês.
A cooperação entre os departamentos está melhorando, bem como a capacidade de realizar
análises de causa raiz. As discussões também estão mudando, olhando sempre para
frente,
e não para trás. Uma consequência natural de Sølve e Hans-Jakob darem mais
responsabilidade aos gerentes de departamento é que eles, por sua vez, precisam dar mais
responsabilidade aos
seus líderes de equipe – imitando o desafio e a relação de apoio com seus
líderes
de equipe e alinhando o desenvolvimento de pessoas com o desenvolvimento de negócios.
E o negócio?
Se você visitar a Mowi Eggesbønes hoje, sem saber nada sobre sua história, você pode pensar
que todas as ferramentas e métodos do lean foram implementados e que “simplesmente funcionaram”.
Mas este não é o caso. À medida que cada departamento e cada gerente avançavam em sua
curva de aprendizagem, o entendimento e a aplicação das ferramentas andavam de mãos dadas.
Hoje, a planta está superando tanto a si mesma, em comparação com alguns anos atrás,
quanto seus pares em todos os KPIs. Ao mesmo tempo, Sølve, Hans-Jakob e o restante da equipe de
liderança pararam completamente de se estressar com as atividades de combate a incêndios. Em vez disso,
eles podem voltar sua atenção para problemas estratégicos e para melhorar o fluxo de valor
completo, trazendo produtos de pesca da mais alta qualidade para as mesas dos consumidores em todo o mundo.
Sølve, Mindaugas, Marcin e Eivind durante a visita para o artigo