"Conseguimos reduzir o setup de 2 horas para 20 minutos! Ótimo!", "Vamos continuar reduzindo mais!" são frases comuns mencionadas após os esforços para a redução do tempo de setup no dia-a-dia.
Sabemos que quanto mais rápido o setup, melhor. Mas será que aqueles "20 minutos" já são suficientes? Como saber se esse tempo é pouco, muito ou suficiente? Será necessário reduzir mais? Qual seria a meta, ou seja, o tempo de setup a ser atingido?
O ideal é ter setup com tempo de troca igual a zero. Mas isto só é possível numa linha de produção com máquinas e equipamentos dimensionados adequadamente e dedicados a um único fluxo de valor. Mas então, como fazer quando isto não for possível?
Este artigo tem como objetivo mostrar como determinar as metas de tempos para setups para que a produção trabalhe em um fluxo nivelado. A partir de uma visão do estado futuro de um fluxo de valor deve-se determinar os tempos alvo de setups assim como os planos de ação para atingi-lo.
O exemplo das Escovas NTL
Vamos analisar o caso de uma empresa fabricante de escovas de aço para uso industrial. Esta fábrica opera em 1 turno de 8 horas com duas paradas de 10 minutos. Foi desenhado o mapa do fluxo de valor para a família de produtos referente à escova circular que possui 5 modelos. Os dois processos básicos são a estamparia compartilhada e uma célula de montagem, com três processos (I, II e III) representados abaixo, com suas respectivas caixas de dados (TC= tempo de ciclo e TR= tempo de troca):
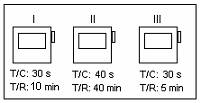
Figura 1 – Célula de montagem.
A estamparia tem um tempo de ciclo de 6,5s com setup de 58 min. Devido à diferença de tempos de ciclo entre a célula e a estamparia, não foi possível estabelecer fluxo entre os dois processos e assim, foi criado um supermercado para puxar a estamparia, conforme mostra a figura 2.
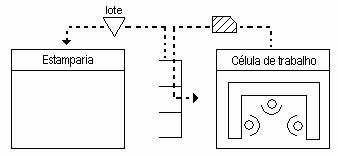
Figura 2 – Fluxo entre a estamparia e célula de trabalho.
A demanda diária desta família de produtos, baseada em uma série histórica de seis meses, para os cinco modelos (A, B, C, D e E), é mostrada na Tabela 1.
Tabela 1 – Demanda diária por modelo.
Modelo |
Demanda diária |
A |
500 |
B |
100 |
C |
50 |
D |
25 |
E |
5 |
Total |
680 |
Análise da célula de trabalho
Apesar de as máquinas estarem fisicamente próximas uma das outras, a célula de montagem não trabalha em fluxo contínuo. Acumulam-se estoques entre um processo e outro. A causa está no elevado tempo de setup no processo II que faz com que se produza grandes lotes de cada modelo. Portanto, devemos reduzí-lo. Mas quanto reduzir? Será que os tempos de setup das outras duas máquinas estão adequados?
O tempo takt da célula em um turno de trabalho é a razão entre o tempo disponível para produção e a demanda do cliente. Sabendo-se que a fábrica opera 8 horas por dia, equivalente a 480 minutos, com intervalo total de 20 minutos e disponibilidade das máquinas de 85%, temos o tempo disponível para produção de (480 min – 20 min)x0,85 = 390 min. Dividindo este valor pela demanda de cada modelo, obtemos seus respectivos tempos takt mostrado na tabela abaixo:
Tabela 2 – Cálculo do tempo takt para cada modelo.
Modelo |
Tempo takt (min/pç) |
A |
390 ÷ 500 = 0,78 (47s) |
B |
390 ÷ 100 = 3,9 |
C |
390 ÷ 50 = 7,8 |
D |
390 ÷ 25 = 15,6 |
E |
390 ÷ 5 = 78 |
Total |
390 ÷ 680 = 0,57 (34s) |
Observando esta tabela, concluímos que a cada 34 segundos, um dos cinco modelos deverá ser produzido pela célula de montagem. Mas afinal, qual modelo produzir primeiro nesta célula? Em que seqüência? Quantos em cada lote? Para responder a isto, precisamos estabelecer regras para a programação da célula de modo a minimizar os estoques intermediários e também de produtos acabados, ou seja, precisamos nivelar a produção.
Nivelar significa produzir todos os itens necessários dentro de um intervalo de tempo (no caso, será um turno de trabalho). Podemos representar graficamente a tabela 2 de outra forma:
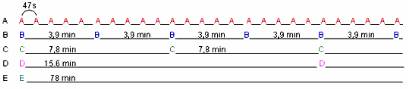
Figura 3 – Nivelamento da produção.
Na figura 3, cada modelo está ordenado e espaçado proporcionalmente ao seu respectivo tempo takt. Se a cada 34s for produzido um modelo na seguinte seqüência:

Ou seja, de acordo com o takt de cada modelo, equivale a produzir o modelo A a cada 47s, B a cada 3,9 min, C a cada 7,8 min e assim por diante.
Agora podemos determinar as metas para a redução do tempo de setup na célula de montagem.
Meta de setup para a célula de trabalho (processo em fluxo)
Na célula de montagem, os modelos fabricados fluirão pelos três processos de acordo com a seqüência apresentada anteriormente, no tempo takt de 34s.
Neste caso, qual seria o tempo necessário para a troca de ferramentas?
Observamos que atualmente, o tempo de setup nos processos I, II e III é respectivamente 10 min, 40 min e 5 min. Sabemos agora qual deve ser a seqüência de produção. Para mudar de A para B e manter o fluxo de uma peça por vez ("one piece flow"), o operador do processo seguinte deverá realizar o setup da máquina enquanto A ainda está sendo processada.
A figura 4 representa a seqüência de produção e o instante em que os setups são realizados para cada modelo.
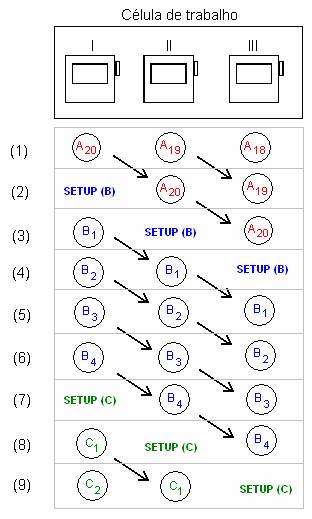
Figura 4 – Preparação em um toque.
Ou seja, em (1), temos o produto A fluindo na linha e sendo processado. Antes de entrar o próximo produto B, deixa-se "fluir 1 vazio" uma única vez na máquina I, como mostrado em (2). É este intervalo de tempo, quando nenhum produto está passando no processo, que será o tempo disponível para o setup da máquina, representado de (3) a (9). Realizado o setup em cada processo dentro do tempo takt (34 segundos), sacrifica-se a produção de apenas uma unidade de peça, porém, mantém-se o fluxo na célula. Este procedimento de troca de ferramentas é chamado de "preparação em um toque".
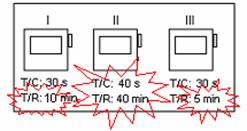
Figura 5 – Kaizen necessários na célula.
Notamos então que há necessidade de realizar os seguintes kaizen para a implementação, conforme representados na figura 5:
- reduzir o tempo de ciclo do processo II (de 40s para 30s) disponibilizando uma folga de 10% em relação ao tempo takt (34s).
- reduzir o tempo de setup no processo I, II e III para 0,57 min (34s);

Figura 6 – Estado futuro na célula.
Para reduzir o tempo de ciclo do processo II, é preciso realizar um estudo detalhado de cada etapa do processo, ou dos elementos de trabalho, junto com os tempos de operação, com o intuito de eliminar desperdícios. Para reduzir o tempo de setup e atingir as metas estabelecidas, pode-se utilizar os métodos de troca rápida de ferramentas desenvolvidos inicialmente por Shigeo Shingo na Toyota na década de 50.
Análise da estamparia
A prensa onde são produzidas as escovas industriais é compartilhada com diversas famílias de produtos. Seu tempo de ciclo é de 6,5s com setup de 58min. O tempo utilizado na produção diária da escova circular é de 73,7 minutos obtidos a partir de 6,5 x 680 ÷ 60. As outras famílias de produtos absorvem 226,3 minutos de trabalho da prensa, perfazendo um total de 300 minutos. Com um tempo de trabalho disponível de 390 minutos, temos apenas 390-300= 90 minutos disponíveis para o setup (desconsiderando neste caso, o tempo para manutenção). Mas com 90 minutos é possível realizar apenas 1 setup de 58 minutos por dia.
Meta de setup na estamparia (processo em lotes)
Para determinar o tempo de setup nesse caso devemos:
- Determinar o tempo disponível para realizar o setup (tempo de trabalho disponível – tempo gasto na produção);
- Saber o número de setups a ser realizado;
- Dividir o resultado de (i) por (ii) obtendo o tempo para o setup da máquina.
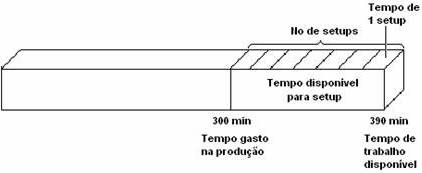
Figura 7 – Determinação do tempo de um setup.
O número de setups necessários é obtido uma vez feito o nivelamento da produção baseado na demanda. Se este número for por exemplo 7 setups, atualmente é necessário 5 dias para realizar todos os setups (58’x7 = 406’ e dividindo por 90’). Isso significa que o supermercado precisa ter um estoque de no mínimo 5 dias para suprir a demanda.
Tendo como meta diminuir este estoque pela metade para reduzir o lead time, devemos então reduzir o tempo de setup pela metade, ou seja, para 29 minutos. Com isso, será possível realizar 14 setups em 5 dias conseguindo 2 rodadas de produção por semana. Em outras palavras, os 7 setups serão feitos em 2,5 dias. Isso duplicará o giro de estoques e reduzirá pela metade o espaço físico ocupado, bem como o tamanho do lote produzido.
Caso a meta seja realizar o nivelamento diário, com 7 setups no turno de trabalho, o tempo de troca a ser atingido deverá ser de 12,8 minutos (90’ ÷ 7).
Conclusão
Ter um setup rápido é um dos passos fundamentais para nivelar a produção. Possibilita-se assim, trabalhar em pequenos lotes e diminuir os estoques, aumentar a flexibilidade e atender mais rapidamente a demanda dos seus clientes.
Ao definir o estado futuro dos fluxos de valor, devemos definir metas para o tempo de setup. Após calcular o tempo takt da família de produto e nivelar a produção, definimos quantos setups serão necessários. Numa linha de montagem ou célula de trabalho, através da "preparação em um toque", garante-se o fluxo contínuo quando não for possível ter o tempo de setup igual a zero. Sempre que houver um processo que não está em fluxo e produz em lotes, como no caso da estamparia, deve-se reduzir o tempo de setup visando uma meta definida, seja para nivelar a produção ou aumentar o giro dos estoques etc. A viabilização da redução requer uma análise de custo beneficio.
De agora em diante, antes de começar um trabalho de redução do tempo de setup, determine antes a meta. "Temos que reduzir o setup nesta máquina para 'x' minutos. Não mais, nem menos!".
Referências
Shingo, Shigeo. Sistema de Troca Rápida de Ferramenta, Bookman, Porto Alegre, 2000.
Smalley, Art. Criando o Sistema Puxado Nivelado, Lean Institute Brasil, 2005.
Toyota Production System, Toyota Motor Corporation, 1987.
Léxico Lean, Lean Institute Brasil, 2003.