Em uma de minhas maiores responsabilidades no Lean Institute Brasil está a coordenação do curso PPFL (Programa Prático de Formação Lean) da indústria. Este curso certamente é um dos mais completos que existem sobre a filosofia lean no mercado. Entretanto, mesmo com muitos conceitos e práticas consolidados durante o treinamento e mesmo com toda orientação dada aos mentorandos, muitos se perguntam: acabou o treinamento, e agora? Será que vou conseguir continuar a implementação na minha empresa? Será que consigo expandir? Será possível disseminar e contagiar a todos com o “lean”?
Bem, essa questão não é exclusiva para o treinamento do PPFL. Na verdade, ela existe sempre que realizamos qualquer tipo de curso ou treinamento. Além disso, ela não é algo tão simples de se responder com um mero sim ou não. Na verdade, tudo depende da condução que será dada a partir de todo o conhecimento e práticas adquiridas no decorrer do curso. Tudo depende também do apoio que você terá dentro de sua organização. Afinal, a alta liderança é parte fundamental da construção da cultura de uma empresa.
Mas indo direto ao ponto, sim, é possível e provável que você consiga sustentar as melhorias e expandir a filosofia lean na sua organização, bem como ampliar sua implementação para diferentes áreas da empresa. Para isso, precisamos entender quais são os passos fundamentais para não deixar o “aprendizado morrer”.
Para ilustrar e deixar de uma maneira mais didática o que acontece durante o PPFL e o que pode (preferencialmente) acontecer após o seu término – para que a organização realmente alcance sua transformação lean –, mostraremos agora a história do Otávio Bortolo, responsável pela área de Controle da Qualidade e Melhoria Contínua da Scholle IPN e um dos participantes do PPFL do segundo semestre de 2019.
Uma história de sustentação e de potencial futuro: Otávio Bortolo sobre a Scholle IPN
A Scholle IPN é uma empresa multinacional que possui diversas plantas distribuídas pelos cinco continentes, dentre elas uma localizada no Brasil, mais especificamente em Vinhedo, estado de São Paulo, onde eu trabalho. A planta de Vinhedo produz diferentes tipos de embalagens plásticas utilizadas para armazenar alimentos líquidos e pastosos processados, tendo por seu carro-chefe o Bag in Box, tipo de embalagem plástica que fica dentro de uma caixa (ou tambores para litragens maiores) para armazenar, por exemplo, bebidas e frutas processadas; e outra linha de produto também importante em relação ao número de vendas que são os chamados cleanpouches e seus conjuntos de tampas e bocais (injetados), que são embalagens utilizadas para colocar, por exemplo, alimentos processados pastosos.
Minha jornada lean começou quando a Scholle IPN me lançou um grande desafio. Por ser uma empresa de mercado com demanda crescente, a Scholle IPN observou que precisava fazer algo para aumentar o seu número de linhas para os próximos dois anos, mas entendia que era primordial garantir essa absorção de demanda sem aumentar o quadro de colaboradores do controle de qualidade e sem perder o nível de qualidade conquistado até então.
Imediatamente, entendi que havia uma grande oportunidade no desafio, porém que também deveria se ter muito cuidado com a área e com as mudanças que nela seriam realizadas, já que qualquer alteração mal pensada poderia gerar uma queda de qualidade nos produtos e perda de certificações importantes já conquistadas pela empresa, e isso seria um verdadeiro desastre para mim e para a empresa.
Estudando e pensando em alternativas que pudessem me ajudar substancialmente nesse momento tão importante, pensei no lean. Já se falava na Scholle IPN sobre a mentalidade enxuta há alguns anos e na área de manufatura alguns conceitos e ferramentas já haviam sido apresentados e implementados, sendo que o GD é o melhor exemplo de lean aplicado e que funciona muito bem na fábrica. Além disso, ocorreram também alguns eventos kaizen, implementação de trabalhos padronizados para testes e set-up de máquinas, uma tentativa de A3, de 5S, entre outros. Entretanto, esses conceitos que vinham sendo implementados pouco a pouco ainda tinham oportunidade de um aprofundamento e maior entendimento da filosofia. O objetivo, então, era estudar.
Sabendo do Programa Prático de Formação Lean, busquei apoio junto à empresa para participar e, assim, aprofundar-me mais na filosofia. Eu realmente acreditava que o lean poderia me ajudar e muito com esse novo desafio. Com total apoio, comecei a desenvolver meu A3, com orientação dos instrutores e gerentes de projetos, utilizando como propósito exatamente o problema que me havia sido apresentado: aumentar a capacidade sem aumentar custos e garantindo a qualidade.
Enfim, o que aconteceu comigo durante o curso foi um propulsionador para minha sustentação e motivação após sua finalização.
1. Primeiro passo: enxergando as causas dos problemas
Após aprender os primeiros conceitos e ver as práticas durante o curso, comecei a ir ao gemba para realmente enxergar como os processos de testes de qualidade funcionavam no dia a dia. Junto com a equipe, mapeamos as etapas do processo dos principais testes, e os passos de cada analista foram cronometrados e desenhados. Criamos um diagrama de espaguete.
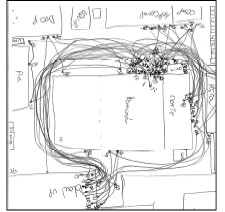
Figura 1: Espaguete de uma hora de trabalho de um analista
Este primeiro passo foi fundamental. Juntos, a equipe e eu pudemos ver oportunidades que nunca teríamos pensado se não tivéssemos seguido esse primeiro grande conceito: fazer gemba. Nossas observações foram:
- O analista observado não parava de andar em nenhum momento.
- O laboratório de teste tinha crescido muito rapidamente, e por isso, os testes não foram instalados pensando em um leiaute adequado para otimizar tempo e para diminuir a carga de esforço de cada analista.
- Havia muito formulário duplicado, ou seja, a maioria era feito à mão e, depois, a pessoa tinha de lançar no computador, o que gerava 30 minutos de retrabalho para cada pessoa, totalizando três horas por dia contando todos os analistas e todos os turnos.
Outra análise proporcionada pela minha ida ao gemba foi em relação aos testes realizados nos setups. Nós percebemos que cada setup levava em média 13 minutos para que fossem realizados todos os testes e a máquina começasse a funcionar. Cada teste foi medido em relação à sua duração e sua frequência diária. Como resultado, observamos que o número de testes por mês ultrapassava dez mil análises.
A partir dessa cronoanálise, chegamos à conclusão de uma nova grande oportunidade para reduzir o tempo dos testes que demoram muito, e isso traria um duplo ganho: além de liberar tempo das pessoas para absorver a nova demanda, isso reduziria o tempo de setup de cada máquina.
2. Segundo passo: implementando as contramedidas
Após nossa análise, a ideia era otimizar a movimentação, excluir o retrabalho de fazer o relatório duas vezes e adequar o leiaute da área de testes. O que era de fácil resolução foi rapidamente solucionado, como a eliminação de esperas para iniciar os testes.
Outro exemplo de ações realizadas foi em relação à adequação dos analistas sobre quem cuida de qual máquina. Antes cada analista cuidava de três máquinas. Observando o leiaute e movimentação e levando em conta que cada analista só tinha conhecimento do que acontecia em suas máquinas, foi mapeada a oportunidade de mudar a forma como isso era feito. Ao invés de cada analista cuidar de um número fixo de máquinas, os analistas cuidariam de um número fixo de testes. Assim, o analista que fica na parte superior cuidaria apenas dos testes que ocorriam por lá, passando por todas as máquinas, e o analista que fica na parte inferior cuidaria dos testes dessa outra parte, passando também por todas as máquinas. Veja na figura abaixo a nova configuração:
Figura 2: Antigo leiaute (à esquerda) e novo leiaute (à direita) da área de testes
Algumas ações imediatas já foram implementadas, como a mudança do local da porta, configuração do leiaute e revisão como um todo; revisão dos requisitos de testes realizados em conformidade com as certificações e os indicadores de qualidade; revisão do método de funcionamento dos equipamentos; e revisão da política de controle de dados. Já outras ações mais demoradas entraram em um plano de execução.
3. Terceiro passo: a colheita dos resultados
Com essas ações simples e sem custos substanciais adicionais à organização, ao final do treinamento (final de 2019), já conseguíamos enxergar muitos resultados positivos:
- 42% de ganhos de tempo na etapa de testes de dados contínuos.
- 25% de ganhos de tempo na etapa de testes funcionais.
Ou seja, conseguimos alcançar os objetivos que tínhamos traçado para o propósito do meu A3 ainda durante o curso. Além disso, eu conseguia enxergar que isso era apenas o começo e que infinitas oportunidades de melhoria surgiram a partir daí.
4. Quarto passo: o meio fio da continuidade do projeto
Acredito que seja aqui que more a dúvida de muitas pessoas e é aqui também que muitas pessoas acabam “se perdendo” e deixando o lean morrer. Quando o treinamento termina e você enxerga os resultados conquistados, você se vê andando num meio fio e se pergunta: e agora? Continuo? Eu consigo? Ou caio fora?
Pela minha experiência e a que vi de muitos participantes do PPFL ao final do curso, a resposta que posso dar é “depois que você é contagiado pelo lean, é muito difícil voltar atrás”. Depois que você passa a conhecer conceitos e práticas do lean não tem mais como você voltar a enxergar as coisas, os desafios e os problemas da mesma forma como antes. E esse é um dos aspectos mais importante que sustenta sua continuidade.
Finalizado o curso, os nossos passos seguintes aqui na Scholle IPN foi o de expansão e disseminação, de forma mais aprofundada, do lean para outras áreas da manufatura (produção e armazém), por meio da capacitação, desenvolvimento das pessoas e implementação de projetos A3, contagiando as equipes e envolvendo-as em todos os processos de melhoria a fim de que se sintam pertencentes e busquem o mesmo objetivo.
Entendemos a necessidade de se aprofundar e de levar a mais e mais pessoas o pensamento A3 como meio de desenvolvimento. Após 9 meses da implementação das oportunidades citadas, já estamos finalizando as implementações do A3 que realizei durante o PPFL, dos demais A3 realizados internamente em outros setores (produção e armazém) e já estamos pensando em uma segunda rodada de treinamentos para que o pensamento A3 se dissemine ainda mais pela organização. Além disso, iniciamos também um programa de Lean Office para que possamos implementar a filosofia Lean também no escritório, algo que é novidade na organização.
Os ganhos que tivemos continuaram e, com a otimização de algumas atividades, já conseguimos notar uma redução significativa no tempo gasto para realização de testes. Como parte final do plano, que acontecerá já em outubro de 2020, os papéis de anotação de testes serão eliminados e novos computadores serão implementados para garantir que os lançamentos sejam feitos diretamente no sistema, eliminando o tempo gasto em duplicidade.
Sustentação e expansão: Iris Bonfanti sobre dicas para continuidade da transformação lean
O interessante que vemos nessa história do Otávio é que essas ações que eles fizeram ainda durante o curso conseguiram atingir o objetivo traçado e trouxeram ainda novas oportunidades de ganhos e melhorias. Além de que, esse movimento dentro da organização motiva muitas pessoas de diferentes níveis a embarcar também em suas jornadas lean, já que todos percebem os benefícios para a empresa e para cada um no seu dia a dia de trabalho.
Pode-se dizer que um dos maiores ganhos, além do quantitativo acima apresentado, é a disseminação da filosofia lean em vários ambientes e níveis hierárquicos e a percepção de que as melhorias proporcionadas pelo lean são benéficas em diferentes sentidos para o indivíduo e para o coletivo.
O PPFL é um curso diferente dos outros porque além de ensinar a aplicar conceitos e ferramentas, ele muda a forma das pessoas enxergarem o mundo, os negócios, a forma de trabalhar, de gerenciar e de lidar com os problemas que surgem. E isso é algo que nunca mais sairá de você. O que não significa que só isso basta para uma transformação total e sustentável na empresa. Por isso, selecionamos algumas dicas essenciais para lhe ajudar na continuidade de sua transformação lean como indivíduo e de sua empresa como negócio:
1. Tornar-se lean requer estudo, disciplina, resiliência e aprofundamento.
Para a jornada lean ter sucesso após o PPFL não pode faltar disciplina e resiliência. Muitas coisas vão fazer você ter motivos para desistir… não é uma tarefa fácil e nem mesmo de curto prazo. Falamos que lean não é corrida de 100m, e sim uma maratona.
2. Aplicar conceitos e ferramentas sem rumo, sem relacionar com o propósito da organização, não faz muito barulho.
Outra coisa muito importante é sempre vincular o uso de alguma ferramenta com o propósito do negócio. Sempre temos que nos perguntar: essa ferramenta vai nos ajudar a resolver qual problema? Resolvendo esse problema estamos mais próximos do nosso propósito?
3. O segredo do lean está na prática.
Uma outra dica que faz com que o lean não perca a chama após o PPFL é praticar, praticar e praticar. Lean só se aprende fazendo. Não tenha medo de errar. Tente! Com certeza o aprendizado será gigantesco.
4. Não importa em qual escala você vai começar. O importante é que você comece.
Muitos começam de forma pequena, escolhendo um “piloto” que seja significativo para o negócio. Isso está perfeitamente adequado. Se bem aplicado, em pouco tempo o lean começará a se expandir e a crescer. Apenas comece.
5. Não tente encontrar respostas prontas.
Não existe uma receita pronta; não existem 10 passos de sucesso para o lean. Crie a sua receita baseada no seu contexto.
6. O lean tem a ver com as pessoas.
Lean é sócio-técnico (na verdade, é muito mais sócio que técnico). Logo, não existe lean se as pessoas não participarem do processo de mudança.
7. Mostre os resultados para obter apoio da alta liderança.
Um ponto que ajuda é mostrar o quanto o lean traz de benefícios (se for possível “valorar” o ganho, melhor ainda). Qual gestor que não gosta de resultados? E o lean traz resultados.