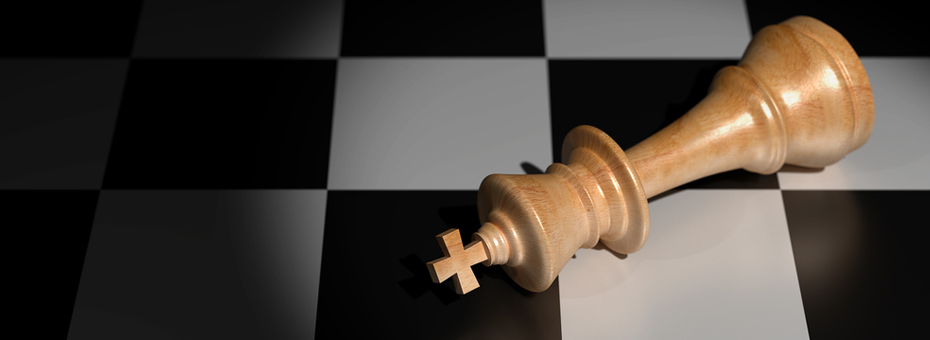
Vamos começar com o fato de que não há estatísticas exatas sobre:
- Quantas empresas começaram a jornada lean.
- Quantas conseguiram se tornar empresas lean.
A maioria [dos consultores lean] diria que o número [de empresas que conseguiram se tornar lean] está entre 5 e 7 por cento
Mesmo assim, acho que se você perguntasse à maioria dos consultores lean ou a outros que estudam o movimento, a maioria diria que o número está entre 5 e 7 por cento. É o que parece para mim. Isso não significa, no entanto, que as outras não obtiveram alguns ganhos com seu trabalho lean; é difícil não ganhar nada. Mas muito poucos fizeram do lean a base de tudo o que fazem em todas as partes da empresa, podendo ser consideradas, então, empresas lean.
Apenas destacar alguns dos principais problemas que vejo acontecendo cada vez mais [incluem]...
Então por que isso acontece? Por que é mais comum o fracasso do que o sucesso? Acho que eu poderia simplificar demais e apenas dizer que lean é "fácil de explicar, mas muito difícil de fazer". Afinal, lean tem a ver com pessoas. São as pessoas que você está tentando converter, e as pessoas são complicadas. Foram elas que construíram o sistema que você tem atualmente, e elas são resistentes à mudança. Isso não é nenhuma surpresa, mas vamos tentar ser mais específicos. A lista de coisas que criam falhas na implementação lean é longa - muito longa para este artigo -, então me deixe apenas destacar alguns dos principais problemas que vejo acontecendo cada vez mais.
[O] foco restrito [na redução de custos] não tem nada a ver com o cliente e com os problemas reais que a empresa precisa solucionar
1. FOCO NA REDUÇÃO DE CUSTOS. Eu diria que entre 90 e 95 por cento de todas as empresas que iniciam a jornada lean fazem isso principalmente como um esforço de redução de custos. Elas não conseguem entender a natureza estratégica do lean e a necessidade de se concentrar na eliminação de desperdícios, a fim de oferecer mais valor a seus clientes. Provavelmente sempre tiveram alguns esforços de redução de custos em andamento, mas pensam que, talvez, a aplicação da caixa de ferramentas lean ajudará a reduzir mais custos mais rapidamente. Então é uma espécie de "reforço das práticas antigas", utilizando apenas algumas novas ferramentas e a terminologia lean. Esse foco restrito não tem nada a ver com o cliente e com os problemas reais que a empresa precisa solucionar, como ter um lead time entre 6 e 8 semanas.
2. COLOCAR O LEAN EM UM SISTEMA EM LOTES. Se você for fazer uma virada lean, precisa entender que tudo deve mudar. Isso vai muito além do que a maioria das empresas consegue entender. Elas só querem reduzir os custos e, então, tentam colocar o lean em um sistema tradicional em lotes sem alterar nada. A equipe de vendas é incitada a sair e obter grandes pedidos e a oferecer descontos por volume. O chão de fábrica produz uma previsão usando o MRP e envia 50% das encomendas na última semana do mês, mesmo que os esforços lean estejam destinados a nivelar a fábrica. As áreas de finanças, RH, TI, desenvolvimento de produtos etc. permanecem iguais. O lean é apenas adicionado como uma das dez melhores estratégias. Isso, obviamente, nunca funcionará e apenas causará confusão em todos os lugares, uma vez que uma parte da organização vai em uma direção totalmente diferente do que todas as outras.
O líder precisa estar no local de trabalho
3. FALTA DE LIDERANÇA. Lean é uma abordagem que prima o "aprender fazendo" e precisa ser liderada pela alta administração na prática. O líder precisa estar no local de trabalho (gemba), participando de eventos kaizen, conversando e ouvindo seu pessoal, aprendendo os detalhes, estabelecendo metas ousadas e empurrando a organização para a frente. Em vez disso, o gerente tradicional tenta continuar "liderando lá de cima", permanecendo no escritório e delegando a virada lean a alguém de sua equipe, como o vice-presidente de operações. "Você tem meu total apoio. Mantenha-me informado".
Quando a empresa tenta mudar sua abordagem em lotes para o mais eficiente fluxo lean, sua própria estrutura fica no caminho e causa muitos problemas
4. SEM MUDANÇA ESTRUTURAL. Mudar de uma organização tradicional para uma organização de fluxo de valor, cujos objetivos de excelência operacional se aproximam da agregação de valor e todo colaborador é responsável por essa agregação de valor, é um passo crítico para levar adiante uma virada lean. Infelizmente, você raramente vê isso. Em vez disso, o fabricante tenta manter todos os equipamentos similares em departamentos funcionais, ou o hospital quer manter sua estrutura por silos, apesar de ter fluxos de valor naturais para coisas como coração, ortopedia, câncer, bebês etc. O resultado é que quando a empresa tenta mudar sua abordagem em lotes para o mais eficiente fluxo lean, sua própria estrutura fica no caminho e causa muitos problemas.
Infelizmente, a abordagem tradicional de gestão por objetivos é mais comum
5. SEM TRABALHO EM EQUIPE. A maioria das pessoas não consegue perceber que o lean é um esporte em equipe. Quando você tenta adequar o tempo takt ao ritmo do cliente, fazer tudo em um fluxo de uma só peça, estabelecer o trabalho padrão e tornar todo o sistema puxado, desde de seus fornecedores até seus clientes usando o princípio lean de "venda-um-faça-um", é melhor que todos estejam na mesma página e trabalhem juntos. Infelizmente, a abordagem tradicional de gestão por objetivos é mais comum. Isso muitas vezes coloca uma parte da empresa contra outra sem que ninguém esteja ciente das contradições. Por exemplo, pedir ao vice-presidente de operações que reduza o estoque e ao vice-presidente de compras que diminua o preço da matéria-prima - o que, claro, ele faz comprando em quantidades enormes, aumentando o estoque.
Implementar lean sem ter o conhecimento internalizado é quase impossível
6. ABRIR MÃO DOS CONSULTORES LEAN MUITO CEDO. Implementar lean sem ter o conhecimento internalizado é quase impossível. Alguém tem que pressioná-lo através das barreiras que o mantêm em seu estado atual. Isso geralmente significa que você precisará de alguma ajuda externa (treinamento). A maioria das empresas faz isso, mas depois de algumas sessões de kaizen, dizem: "ah, entendi". Então elas dispensam os consultores com a ideia equivocada de que vão economizar custos e, antes de perceber, voltam ao estado inicial.
Lista de razões por que as empresas falham em se tornar empresas lean é longa. Mas não se desanime. [...] Você pode [...] fazer algo sobre seus resultados futuros melhorando seus processos
7. OUTROS PROBLEMAS. Como eu disse, a lista de razões por que as empresas falham é longa. Alguns outros itens são:
- Tentar implementar lean e manter uma abordagem padrão tradicional de contabilidade de custos, mesmo que a contabilidade de custos padrão incentive todas as coisas que você está tentando se livrar com o lean.
- Continuar com o foco em "ganhar o mês" em vez de se concentrar em remover o desperdício dos processos que criaram os resultados do mês passado para que os resultados futuros possam ser melhores.
- Utilizar um ritmo muito lento, como fazer um kaizen a cada seis semanas e concentrar-se em pequenos problemas isolados, em vez das principais famílias de produtos.
- Continuar tentando solucionar problemas com automação e TI, o que muitas vezes resulta em apenas automatizar o desperdício.
De qualquer forma, acho que você entendeu. A lista de razões por que as empresas falham em se tornar empresas lean é longa. Mas não se desanime. Apenas tente evitar todas essas armadilhas e você terá um grande sucesso. Lembre-se, concentre-se em seu processo e não em seus resultados. Seus resultados já aconteceram. Você não pode fazer nada sobre eles agora. Você pode, no entanto, fazer algo sobre seus resultados futuros melhorando seus processos.