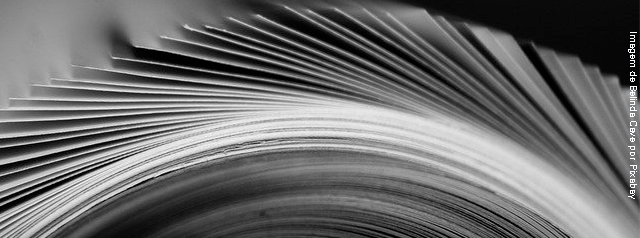
Este artigo mostra a implementação de células de manufatura em uma empresa gráfica, substituindo o layout linear pelo layout celular, onde foi projetada e implementada uma “célula-piloto” para o processo de montagem de cadernos.
A implementação de uma célula de manufatura em caráter de “projeto-piloto”
A empresa objeto do estudo de caso apresenta um sistema de produção com características do modelo clássico taylorista-fordista, facilmente identificado por aspectos do tipo: utilização de layout linear, operadores especializados (monotarefa), inflexibilidade da capacidade produtiva quanto à variação da demanda, produção em grandes lotes e controle de qualidade no produto acabado.
Os itens produzidos estão agrupados em quatro famílias: impressos padronizados, livros fiscais, formulários contínuos e cadernos.
O processo encontra-se dividido em cinco etapas de fabricação, a saber: impressão, preparação (de capas e impressos padronizados), corte, montagem de livros fiscais e montagem de cadernos. Para fins desse artigo, apenas a última etapa descrita será considerada.
A linha de montagem de cadernos
O caderno é composto pelos seguintes itens: capa, miolo, espiral, adesivo e plástico. O processo de montagem consiste na execução de uma seqüência de etapas operacionais (Figura 1) realizadas numa linha de montagem (Figura 2). Essa linha ocupa uma área de 155,13m2, produz um volume médio diário de 2.647 unidades em um único turno de 8 horas, com um efetivo de 9 pessoas (MOD).
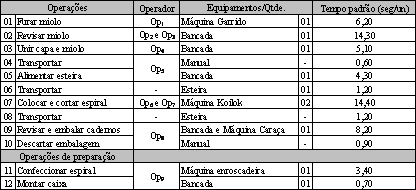
Figura 1 – Operações do processo de montagem de cadernos – arranjo físico linear
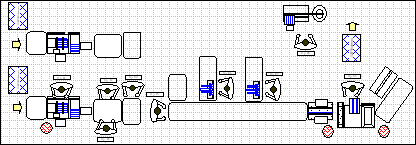
Figura 2 – Lay-out: arranjo físico linear
No arranjo físico linear (Figura 2) os operadores trabalham sentados, em regime de monotarefa; a disposição dos postos de trabalho dificulta o agrupamento de operações, contribuindo para uma sub-utilização da mão-de-obra (Figura 3); o fluxo de produção é irregular devido ao desbalanceamento dos recursos; e os estoques intermediários (WIP) internos contribuem para o aumento do lead-time de fabricação do produto.
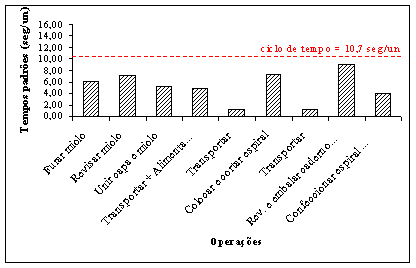
Figura 3 – Agrupamento de operações aplicado ao arranjo físico linear
Observa-se na Figura 3, que os operadores têm grande capacidade ociosa em relação ao Takt-time (Ciclo de tempo), o que resulta na formação de estoques de materiais entre operações (WIP), estes por sua vez, influem diretamente no aumento do tempo de atravessamento do produto no processo produtivo, na superprodução quantitativa e na espera dos lotes na fila de recursos.
Implementação da proposta de arranjo celular
Com base nos pedidos de clientes (vendas) determinou-se uma demanda de 2.700 unidades/dia para os produtos processados na célula de montagem de cadernos. O ciclo de tempo (takt-time) que é o quociente das horas disponíveis/dia pela produção necessária/dia (MONDEN, 1984) foi determinado em 10,7 segundos/unidade produzida.
Assim, temos:

Na seqüência, procedeu-se uma análise sistemática das operações visando a criação do “fluxo de valor operacional”, e o aumento da taxa de utilização da mão-de-obra e dos equipamentos. Nesse sentido, foram tomadas as seguintes ações:
- Agrupamento das operações “furar miolo” e “confeccionar espiral”;
- Agrupamento das operações “revisar miolo” e “unir capa e miolo”;
- Agrupamento da operação “montar caixa” com as operações “revisar e embalar cadernos” e “descartar embalagem”;
- Separação dos elementos manual-máquina na operação “colocar e cortar espiral” (Conceito JIDOKA).
Essa análise resultou numa nova seqüência operacional (Figura 4) através da qual constatamos as seguintes melhorias:
• Redução de mão-de-obra;
• Redução de tempo padrão;
• Redução de equipamentos;
• Redução de operações;
• Eliminação de transportes.
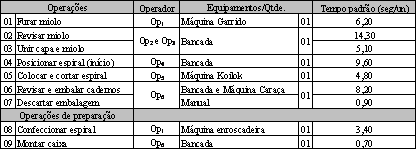
Figura 4 – Operações do processo de montagem de cadernos
Dessa forma, observou-se um processo mais equilibrado (Figura 5), com as operações balanceadas e próximas ao ciclo de tempo (takt-time). Esse novo agrupamento permitiu estabelecer e manter um ritmo constante de trabalho através do fluxo contínuo e possibilitou o monitoramento ao longo do turno de trabalho, garantindo que a demanda puxada pelo cliente fosse atendida diariamente.
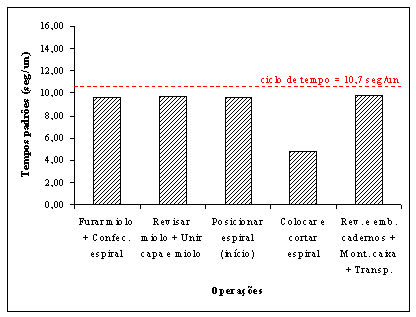
Figura 5 – Agrupamento de operações aplicado ao arranjo físico celular
Os recursos mão-de-obra, equipamentos e chão-de-fábrica, foram otimizados, uma vez que os postos de trabalhos foram aproximados e dispostos em configuração “u”. A Figura 6 mostra a nova disposição física ocupando uma área de 102,27m2.
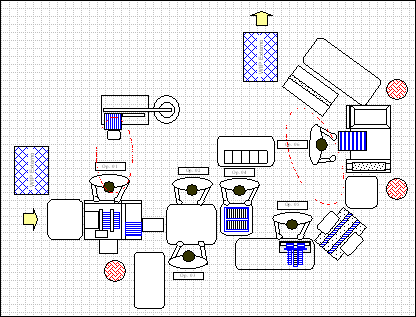
Figura 6 – Arranjo físico celular
Após a elaboração das propostas de balanceamento de operações e arranjo físico celular deu-se início à implementação. Nessa etapa foram realizados os ajustes necessários ao perfeito funcionamento do sistema incluindo adaptação dos equipamentos, criação de dispositivos e treinamento multifuncional dos colaboradores.
Uma vez realizados os ajustes a célula passou a fazer parte do processo produtivo em condições normais de trabalho, sendo avaliada através dos indicadores implantados.
Análise dos resultados
A Figura 7 apresenta um comparativo entre uma linha e a célula de montagem de cadernos, tomando por base os indicadores escolhidos. Os indicadores propriamente ditos se comportam da seguinte forma: a produtividade da mão-de-obra aumentou de 36,8 para 52,1 cadernos/homem-hora representando uma evolução de 41,6%. A produtividade do chão-de-fábrica também apresentou um crescimento, passando de 17,4 para 26,4 cadernos/m2, representando um incremento de 51,7%.
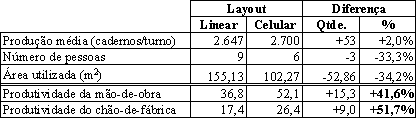
Figura 7 – Comparativo layout linear X layout celular
Outros ganhos também puderam ser percebidos quando da implementação da célula, sendo alguns deles tangíveis e outros intangíveis. Embora não tenham sido objeto de estudo deste trabalho é importante comentarmos.
De ordem quantitativa houve uma redução nos estoques existentes entre os postos de trabalho passando, com exceção da primeira operação (furar miolo), para um lote unitário; o tempo de atravessamento também foi reduzido em virtude da eliminação dos lotes intermediários, da espera e movimentação; redução do consumo de energia elétrica e custos de manutenção devido à retirada de alguns equipamentos do processo. De natureza qualitativa pôde-se observar um aumento da motivação dos colaboradores em função do enriquecimento da tarefa; uma melhor qualidade percebida do produto final e o house-keeping do setor também melhorou consideravelmente.
Viabilidade da implementação Lean
Com base na experiência apresentada, vivida pelo autor, pode-se concluir que os indicadores escolhidos para fundamentar a análise comparativa (mão-de-obra e chão-de-fábrica), embora não avaliem por completo toda a eficiência do layout celular, traduzem de certa forma os benefícios gerados por essa abordagem no processo produtivo.
Referências Bibliográficas:
CORRÊA, Henrique L. & GIANESI, Irineu G. N. (1993) - Just In Time, MRP II e OPT: um enfoque estratégico. São Paulo: Atlas.
GHINATO, P. (2000) - Publicado como 2o. cap. do Livro Produção & Competitividade: Aplicações e Inovações, Ed.: Adiel T. de Almeida & Fernando M. C. Souza, Edit. da UFPE, Recife.
KARLSSON, C. & AHLSTRÖM , P. (1996) – Assessing changes towards lean production. International Journal of Operations & Production Management. Vol. 16, n.2, p. 24-41.
MONDEN, Yasuhiro (1984) – Produção sem estoques: uma abordagem prática do Sistema de Produção da Toyota. São Paulo: IMAM.
OHNO, Taiichi (1997) - O Sistema Toyota de Produção: além da produção em larga escala. Porto Alegre: Bookman.
TUBINO, Dalvio Ferrari (1999) – Sistemas de Produção: a produtividade no chão de fábrica. Porto Alegre: Bookman.