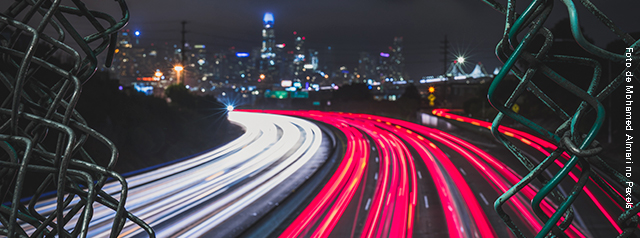
Quando eu era CFO (Chief Financial Officer) da Lantech (Louisville, KY), ajudei a adaptar o sistema de tecnologia de informação ao ambiente de manufatura lean da empresa. Nossa jornada (que é a base do meu livro com Duane Jones, “Easier, Simpler, Faster: Systems Strategy for Lean IT”, Productivity Press) fornece um exemplo de uma conversão lean para os sistemas de tecnologia de informação.
Como a produção lean não necessita de uma programação complexa da produção, planejamento das necessidades de materiais ou a contabilidade padrão dos custos, não é fundamental ter TI e um ERP rodando tais processos. Por outro lado, você irá precisar se adaptar inquestionavelmente aos produtos ERP existentes para satisfazer as novas necessidades de informação em um ambiente lean, especificamente e especialmente para o processamento dos pedidos, o faturamento dos clientes e os fechamentos contábeis. O ERP também cria novas possibilidades para coletar informações dos clientes, o que é vital para uma empresa lean.
Um sistema ERP é um conjunto de operações integradas e computadorizadas que incluem idealmente toda faceta de toda as operações que a empresa desempenha. O Planejamento das Necessidades de Materiais (MRP) é geralmente um subsistema do sistema ERP, embora seja algumas vezes um sistema isolado com uma funcionalidade limitada ao MRP. Na sua forma mais completa, o MRP é um programa que determina o que você quer produzir e quando. Ele coleta informações dos pedidos de vendas, os valores mínimos dos estoques disponíveis, ou diversos meios artificiais que você usa para informar o processo para fabricar um determinado item. O MRP então determina a matéria prima que você precisa, quais itens você precisa manufaturar, quais equipamentos precisa, e qual a mão de obra necessária. Uma vez com essas informações, o MRP compara os dois primeiros itens com o que você possui de matéria prima, o que você tem em pedidos, o que você já tem em estoque, o que você está produzindo, quais os equipamentos que possui, e quais os recursos humanos você tem disponível. Em essência, o produto de um MRP é uma programação: uma lista que sugere o que você precisa fazer e quando deveria fazer, a fim de produzir o que precisa quando precisa.
O único cálculo que o MRP realmente faz é comparar o que você quer com o que você possui, e isso determina os recursos necessários para ter o produto para o consumidor. A maioria dos MRP pode provavelmente ser configurado para automaticamente disparar ordens de compra ou notificar os funcionários para os tempos de inicio e as tarefas. A grande maioria das empresas recebe as sugestões do MRP e agem sobre elas sem muita revisão. No entanto, rodar uma empresa com um sistema totalmente automático é um grande risco. Embora o MRP possa manter as atividades fluindo em ordem, a pergunta é; “a que custo?” Já que os clientes apenas desejam pagar pelo o que eles pensam que é o valor de um produto, temos que encontrar maneiras para reduzir os custos para nos tornarmos mais rentáveis. O MRP usado na forma tradicional não irá dar suporte para essa redução de custos até que seja integrado com o sistema lean.
Os cálculos de mão de obra são a primeira coisa a ser retirada do MRP. Com o fluxo de uma peça, manufatura em célula, a programação e o monitoramento dos trabalhadores torna-se muito mais simples. Em um ambiente puxado, calcule a taxa de demanda do cliente. Por exemplo, uma taxa de entrada para um produto A requer uma produção de dez por dia. Porque a nossa linha de montagem exige dez operários para construir dez máquinas por dia, programamos dez operários para trabalhar naquela linha todo dia. Não precisamos de um relatório gerado por um sistema para saber que precisamos de dez pessoas, nem precisamos que essas pessoas apontem seu tempo de trabalho no sistema para saber que eles estão trabalhando todo dia. O fato de o produto estar sendo carregado no caminhão conforme o programado é uma prova suficiente.
Talvez você se pergunte como utilizar a mão de obra efetivamente sem uma programação da capacidade e das necessidades. Um objetivo das operações lean é construir um produto de cada vez para o cliente, e isso coloca nosso pessoal de manufatura em sintonia com vendas. Se vendas aumentar além dos dez dias padrão, aqueles dez trabalhadores irão trabalhar fazendo horas extras para manufaturar o pedido, ou então adicionar algumas pessoas extras a linha. O único ponto crítico da fabricação é a programação das horas de trabalho baseada nas vendas reais, não por sugestões do relatório gerado pelo MRP. Se alguma flutuação no lead time é aceitável, o estoque de produtos acabados não será necessário. Para empresas que não possuem a habilidade de produzir para os lead times da demanda do cliente, manter algum estoque em mãos poderia ser necessário. Do mesmo modo, a programação do processo deve ser simples.
Algumas empresas podem estar preocupadas que elas não podem obter custos da mão de obra precisos se elas não fazem a programação e o controle. A solução para isso é simples: saiba quantos operários é necessário para fabricar o seu produto, e você saberá os custos da mão de obra. No exemplo acima, é necessário dez operários para construir dez produtos. Mesmo que o trabalho varie para diferentes produtos, os preços estão estabelecidos. As variações no trabalho nunca serão severas o suficiente para merecer uma mudança no preço – pelo menos não sem uma revisão – então não precisamos nos preocupar em apontar e atualizar diariamente as horas de trabalho no sistema MRP.
Ocasionalmente gostamos de ter mais detalhes de uma máquina especifica, mas é mais barato tratar com a aquela máquina como exceção, ao invés de monitorar cada máquina na linha. Não há valor significativo em programar ou monitorar a capacidade de um equipamento como fluxo de uma só peça, pois o fluxo de fabricação define que você coloca equipamentos onde faz sentido e utiliza-os quando necessário. A máquina permanece ociosa quando você não necessita dela, porque o pensamento lean não tenta atingir 100% da capacidade de uso. De fato, isso seria um sinal de desperdício – produzir coisas independentemente da demanda do cliente. Se uma empresa tem máquina que estão atingindo a plena capacidade, a teoria das restrições (TOC) é uma excelente maneira para otimizar a produção da empresa, até que o desperdício no uso das máquinas bloqueia a capacidade, ou equipamentos adicionais estejam disponíveis para atender as necessidades da demanda dos clientes.
Antes de adotar o fluxo de uma só peça, as empresas dependiam quase exclusivamente do MRP para gerar ordens de compra para o reabastecimento de materiais. Implementar o kanban muda tudo isso, relegando o MRP a um papel menos importante em termos de volume. Na medida em que você implementa o kanban para garantir a reposição de material, e entrega itens kanban fora dos processos normais de compra, você precisará adaptar o MRP. Essas mudanças são significativas e são uma importante questão do sistema de informação. Como o kanban externo (ou baseado nos fornecedores) é um método de reabastecimento visual e automático, os itens em kanban serão excluídos do processo comum do MRP. Quando o processo kanban estiver integrado com o sistema ERP, simplesmente defina um sistema para ignorar todos os itens em kanban. Como resultado, nenhuma ordem de compra será sugerida e/ou criada para revisão. O material está sempre Just-in-time.
Através da utilização de kanban externo da Lantech com um produto definido pelo cliente, mais de 90% do material é pedido e enviado sem o acompanhamento próximo da gerência, enquanto continua mantendo níveis mínimos de estoque. Em 2005, a Lantech gerou 9.274.879 itens na produção em WIP. Apenas 6,5% desses itens era programado pelo MRP. Para o produto com maior volume, o percentual caia para menos de 3%.
Guia dos treze princípios de sistema de informação
Duane Jones e eu documentamos esses princípios na Lantech. Eles estão por detrás de todas as decisões relativas à adaptação do sistema TI que fizemos para o ambiente lean:
- Automatize apenas se for fácil, rápido e complementar a sua cultura.
- Construa comunização para aumentar a visibilidade e o acesso à informação.
- O objetivo principal da segurança é evitar a corrupção de dados e fornecer acesso à informação.
- Nada dura para sempre.
- Inflexibilidade do sistema e de softwares pode ser o grande inibidor da mudança.
- Instruções simples são melhores.
- Teclar importa para os usuários poderosos.
- Descubra tudo que consiga sobre o seu cliente.
- Arquive a historia do cliente, arrume a sua casa em transações internas.
- Capture a informação uma vez e pronto.
- Use a comunização para criar uma rodovia de informação.
- A produtividade de todos é mais importante que a produtividade individual.
- Grandes armazéns de dados são fáceis de manipular.
Devemos dar atenção especial às peças que não são padronizadas ou pouco solicitadas que tornam o kanban inviável. Em alguns casos, melhores utilizações para o MRP são encontradas. O MRP explode a lista de materiais para aquele produto até o nível da compra. Naturalmente, excluímos todos os itens em kanban, pois eles seriam entregues através de seus próprios processos. O programador é deixado com apenas uma pequena lista dos itens que não estão no kanban e são requeridos para montar o produto em questão. O programa MRP lista a quantidade disponível e os requerimentos atuais de cada item, assim como os vários fornecedores, custos e lead times. Para comprar um item, o programador aponta e clica os itens na tela do computador e define uma data de entrega. O programador finaliza o processo e envia múltiplas ordens de compra para vários fornecedores. A etapa final do processo acontece quando as peças chegam na doca de recebimento um dia antes da manufatura requerê-las, com uma observação anexa a cada uma indicando o exato pedido de vendas e o produto para o qual o item foi comprado.
É difícil mensurar a melhoria de produtividade adquirida com a utilização simplificada da ferramenta MRP. O que é certo é a melhoria de comunicação através da eliminação de desperdícios, especialmente do desperdício número um, a superprodução de informação. O usuário agora pode manter informações para apenas um pedido. Sem essa ferramenta, a equipe de compras teria que revisar diariamente as sugestões do MRP sobre quais peças comprar e quando comprar. Finalmente, eles iriam agir cegamente ou falar com muita gente até que alguém soubesse. Agora, programadores experientes colocam ordens de compra no chão de fábrica.
O MRP era visto como indispensável, porém algumas vezes era visto com excessivamente demandante, pois emitiu sugestões que deveriam ser cumpridas à risca. As empresas dependem da precisão e acuracidade do sistema, e o sistema tem que assegurar que tudo está sendo propriamente mantido e rígido. Se o sistema tivesse um problema, no entanto, poderia perturbar tudo, algumas vezes com sérias repercussões. Hoje, o papel do MRP mudou. Não mais dita o que deve ser feito. Ao invés disso, ele foi relegado para o papel de uma rede de segurança confiável.
Continuamos a utilizar o ERP para tornar nossos processos mais lean, mas muitas das funções realizadas agora são guiadas por kanban ao invés do MRP. Ao fazer a mudança, eliminamos o procedimento de compra da maioria dos processos padrão, liberando o pessoal de compras para efetivamente gerenciar os fornecedores.
Traduzido por Diogo Kosaka