Na Vilkun, temos trabalhado em um produto inovador nos últimos 15 anos. Nossa missão é selecionar as melhores frutas chilenas e transformá-las em frutas desidratadas, liofilizadas e congeladas que possam ser usadas como ingredientes. Não há muitas referências para esse tipo de produto, tanto em termos de receita quanto em processo de fabricação: na verdade, quando entrei na empresa, tive dificuldade para entender sua aplicação.
Do ponto de vista de equipamentos, nossa planta de 140 pessoas no sul do Chile é bastante avançada, mas isso não nos impediu de enfrentar uma série de problemas em nosso processo antes da chegada do pensamento lean à nossa organização em 2020. Nossos principais problemas eram os altos custos operacionais e a falta de padronização entre os diferentes turnos, o que afetava a nossa competitividade.
O Mapa do Fluxo de Valor que desenhamos – o primeiro passo real em nossa jornada lean – revelou que os turnos não funcionavam da mesma maneira: havia “instrutivos” em vigor (procedimentos operacionais padrão, por assim dizer), mas as pessoas não os seguiam na prática. O MFV também nos mostrou que tínhamos muito trabalho em andamento na área de secagem e que muitas das caixas que chegavam à área de embalagem eram rejeitadas por problemas de qualidade. Tínhamos que fazer alguma coisa, e o lean apareceu como uma grande oportunidade de trazer organização para o nosso trabalho.
Assim, desenvolvemos vários experimentos e projetos-piloto. No início, adicionamos todos os problemas que encontramos à lista de “a resolver”, mas em pouco tempo percebemos que não poderíamos lidar com tudo de uma vez. Decidimos priorizar aqueles problemas que, se resolvidos, nos dariam mais valor. Nesse ponto, criamos equipes de trabalho, cada uma das quais identificaria e aplicaria uma contramedida ao problema em que estava focando. Foi assim que realmente começamos a fazer mudanças.
As equipes de trabalho começaram a trabalhar em três áreas-chave nas quais estávamos enfrentando problemas críticos para os negócios. Em particular, focaram em:
- A padronização da receita para garantir o melhor rendimento possível de matéria-prima e maior estabilidade no produto (que deve manter suas características nutricionais e de textura até chegar à mesa de jantar do cliente). Fizemos vários experimentos com diferentes parâmetros e alteramos o processo até chegarmos a uma receita que nos agradava (também conseguimos reduzir nosso consumo de matéria-prima em 15%).
- A criação de um supermercado para garantir a disponibilidade da calda e evitar atrasos no processo. Analisamos o consumo, definimos o estoque crítico que precisamos ter sempre disponível e construímos um sistema de reabastecimento baseado na puxada.
- Na área de embalagens, tentamos resolver os problemas de retrabalho que encontramos aumentando o número de “prontos para exportar na primeira tentativa” em aproximadamente 40%. Ao tentarmos fazer isso, percebemos que o retrabalho necessário para corrigir as caixas defeituosas era resultado claro da variação entre os turnos. Usamos um Pareto para analisar os principais motivos das caixas defeituosas e para tentar adequar o produto para expedição antes de embalá-lo, evitando, assim, o retrabalho. Ajudar as pessoas a entender o desperdício que se escondia nessas caixas rejeitadas foi um divisor de águas na jornada lean da Vilkun.
Um obstáculo no caminho
Ficamos satisfeitos com a nossa receita. Ela foi o resultado de vários experimentos e ciclos PDCA (e de muito trabalho). Por fim, conseguimos identificar a receita e padronizá-la em nossos turnos. Melhoramos o rendimento e estávamos bastante confiantes com o que havíamos alcançado, apesar das dificuldades inerentes ao trabalho com um produto natural tão inovador como esse – que é notoriamente difícil de manusear em um ambiente fabril.
Quando secávamos o produto, ele normalmente estava dentro dos parâmetros, mas quando ele era inspecionado em nosso armazém, éramos informados de que ele não era fluido o suficiente para embalar. Tivemos que reduzir a quantidade de água nele. Esse foi um duro golpe para a equipe. Pensávamos que estávamos indo tão bem! Além disso, com a nova restrição, simplesmente não conseguíamos lançar o produto. Nossa fábrica funciona 24 horas por dia, 7 dias por semana, e toda vez que mexíamos na receita, tínhamos que interromper o processo de produção. Os pedidos começaram a se acumular, e o departamento de vendas começou a nos pressionar.
Ficou claro que não podíamos mais procrastinar. Tivemos que voltar à estaca zero, não importando o quão frustrante fosse isso. Marcelo Pinto, do Lean Institute Chile, estava no local naquele dia, treinando uma de nossas equipes. Ele nos ajudou a organizar nossos pensamentos, e nos próximos dias, conseguimos redesenhar o processo de secagem. Eventualmente, o trabalho duro valeu a pena, e conseguimos melhorar a eficiência na secagem. Era tudo uma questão de persistência! Recebemos grande apoio durante a jornada e percebemos que compartilhar o ônus de descobrir as diferentes etapas do processo provou ser a abordagem correta. Foi aí que aprendemos uma lição importante: podemos resolver qualquer problema se trabalharmos juntos e o abordarmos cientificamente.
Outra coisa que realmente me impressiona em nossa jornada até hoje é que conseguimos alcançar muito em um curto espaço de tempo e sem investimento. Experimentos simples podem ter um impacto enorme, e para nosso pessoal, é tranquilizador saber que podemos tentar algo novo e, se as coisas não derem certo, apenas voltar atrás sem desperdiçar dinheiro.
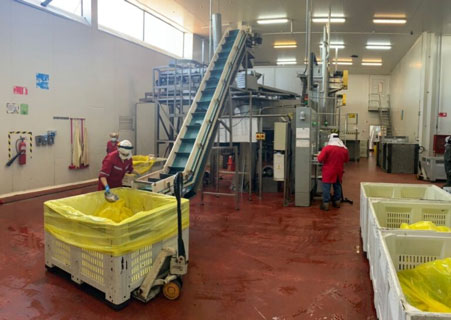
Lean: uma revelação na transformação lean da Vilkun
Com o pensamento lean, descobrimos uma nova forma de trabalhar, na qual colaboramos na solução de problemas, dando a todos uma responsabilidade clara e acompanhando o que discutimos.
O gerenciamento diário foi absolutamente fundamental para nós, para garantir que pudéssemos sustentar os resultados alcançados e continuar usando as ferramentas de forma eficaz. Agora, nós o adotamos como nossa forma de trabalhar, com o departamento de embalagem particularmente ansioso para interiorizá-lo.
As pessoas se animaram com o lean rapidamente, embora houvesse alguns mal-entendidos no início, e as mudanças começassem a competir umas com as outras. Eles pensavam que queríamos que eles simplesmente produzissem mais, então tivemos que explicar a eles que a ideia era realizar a ação corretiva adequada o mais cedo possível para que pudéssemos corrigir os problemas antes que eles se tornassem grandes demais para serem abordados. Hoje todo mundo entende isso. A atmosfera no trabalho também melhorou muito.
Para garantir que nosso pessoal estivesse conectado, ensinamos os princípios e as práticas lean para 15 participantes-chave do negócio – incluindo supervisores e gerentes de área – para que eles pudessem compartilhar seus aprendizados com o restante da equipe. Mas a mudança que experimentamos não teria sido possível sem uma mudança fundamental na cultura da liderança: hoje, a equipe de liderança da Vilkun desafia as pessoas da linha de frente mais do que nunca, mas também fornece as ferramentas necessárias para fazer seu trabalho da melhor maneira possível. Entendemos que as pessoas vêm trabalhar não apenas para operar uma máquina ou completar uma tarefa, mas para participar da melhoria de processos.
O lean nos ensinou a importância de incentivar as pessoas a fazer perguntas, compartilhar suas opiniões e sempre destacar os problemas. Afinal, eles estão em melhor posição para sugerir maneiras de melhorar o processo, porque eles o conhecem melhor. Quando nossa equipe viu que não tinha problema mudar as coisas e que os líderes estavam lá para apoiá-los e responder as suas perguntas, eles abraçaram a nova maneira de trabalhar e nunca mais olharam para trás.